Sterownik PLC - czym jest i do czego służy?
Dawid Pawlak , 1 lutego 2024
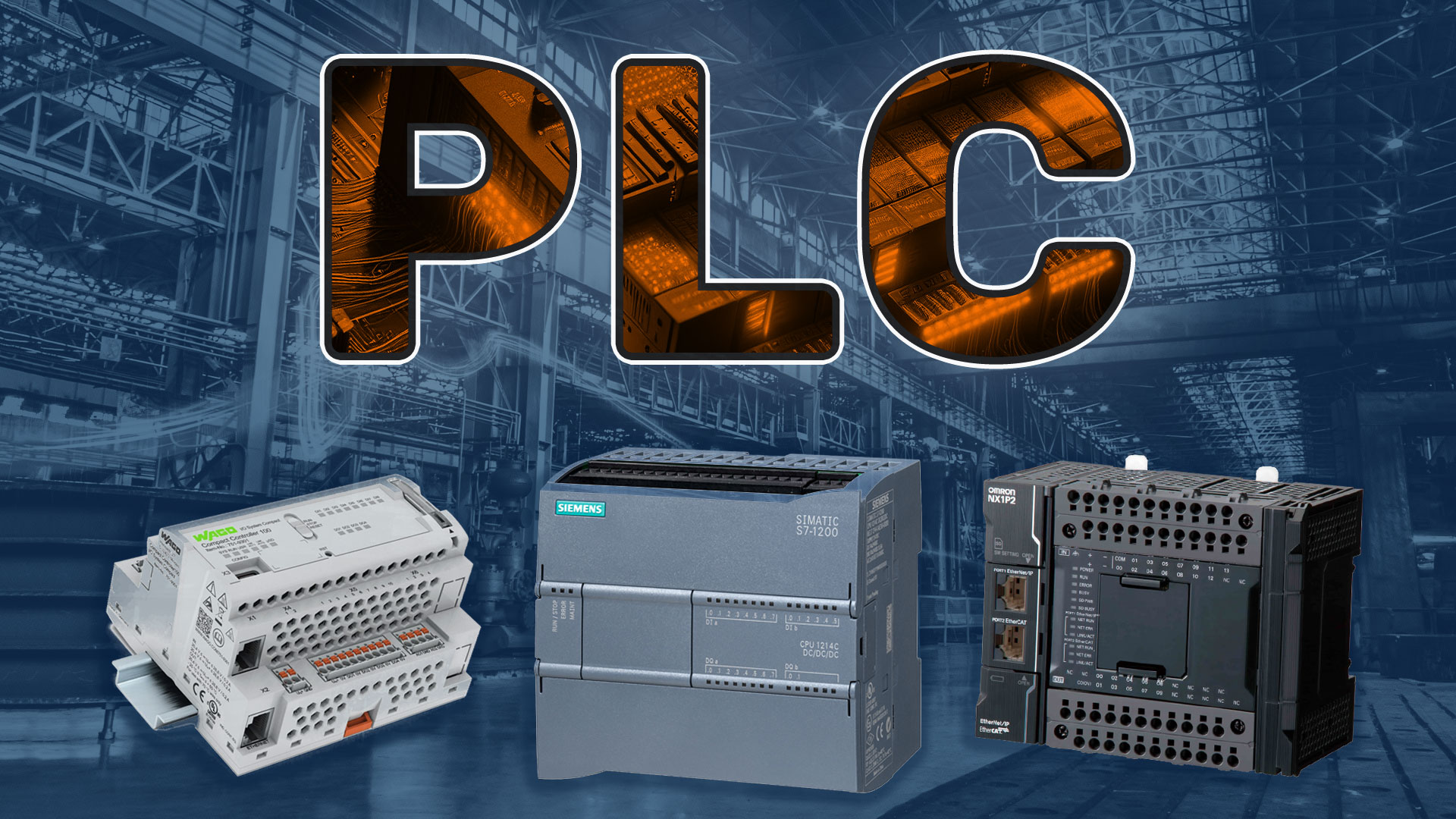
Sterownik PLC w rozwinięciu oznacza programowalny sterownik logiczny (z ang. Programmable Logic Controller) i są to urządzenia mikroprocesorowe wykorzystywane w przemyśle do sterowania pracą maszyn i innych urządzeń technologicznych. Sterownik ten zbiera dane z czujników, przycisków, innych systemów i względem otrzymanych danych wykonuje program logiczny, a potem steruje urządzeniami wykonawczymi w systemie sterowania.
Świat przed sterownikami PLC
Przed stworzeniem sterowników PLC, maszyny były sterowane przez obwody przekaźników i styczników. Jednak z czasem logika działania urządzeń stała się coraz bardziej skomplikowana co powodowało ciągły rozrost szaf elektrycznych i utrudniało to serwisowanie, utrzymywanie i zwiększało koszty tego typu maszyn. Bardzo trudna była diagnostyka problemu i ewentualne zmiany w logice działania.
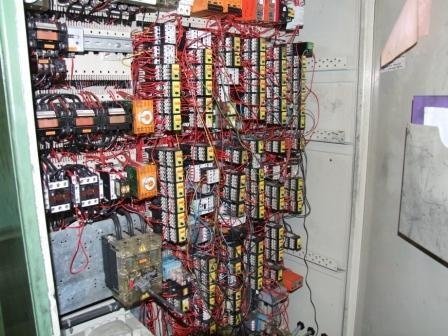
Szafa elektryczna zbudowana na bazie przekaźników i styczników przed pojawieniem się sterowników PLC.
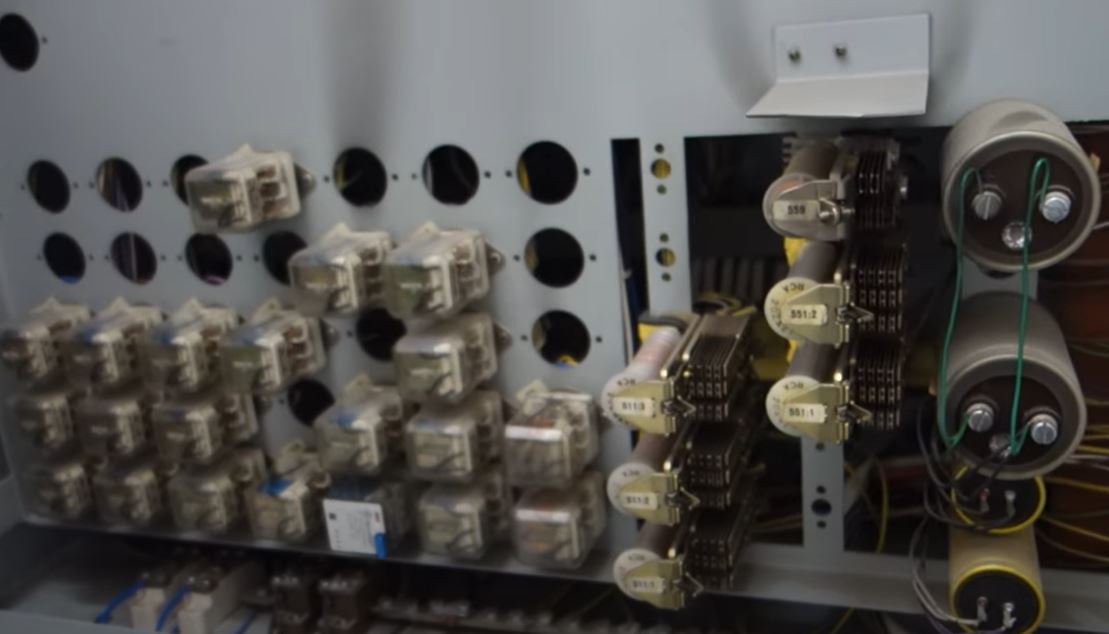
Sterownik windy, zbudowany z przekaźników, pomimo swojej prostej logiki, wymaga dużej liczby elementów.
Projektowanie nawet prostego algorytmu obsługi windy wymagało zastosowania dużej liczby przekaźników, których ilość rosła wraz z liczbą obsługiwanych pięter. W algorytmie sterującym to przekaźniki pełniły funkcję "pamięci", a ich rola polegała między innymi na zapamiętaniu faktu wciśnięcia przycisku na konkretnym piętrze.
Same przekaźniki i styczniki były elementami posiadającymi ruchome części, które z biegiem czasu ulegały zużyciu i awariom, co prowadziło do błędnego działania algorytmu sterującego. To z kolei generowało przestoje i wymagało żmudnego procesu identyfikacji, który z elementów uległ awarii.
Historia sterowników PLC
Pierwszy sterownik PLC został stworzony przez firmę Modicon model 084 w 1969 roku w USA. Potrafił zastąpić setki, a nawet i tysiące przekaźników odpowiedzialnych za wcześniejszą logikę. Potem we wczesnych latach 70 firma Allen Bradley zaprezentowała swój sterownik i spopularyzowała nazywanie urządzeń tego typu programowalnym sterownikiem logicznym. Już po 10 latach od pierwszego sterownika zaczynały być wdrażane pierwsze protokoły komunikacyjne pozwalając na redukcje okablowania w rozległych maszynach. Z biegiem lat zapisano normę międzynarodową IEC 61131, która ustandaryzowała m.in.: właściwości sterowników PLC, zasady komunikacji, języki programowania. Do programowania służyły specjalistyczne panele programowania z przyciskami funkcyjnym lub terminale, które były jeszcze używane do połowy lat 90. Potem zaczęły powstawać pierwsze środowiska programistyczne upraszczając pisanie programu PLC za pomocą komputera.
W drugiej połowie lat 90 mocno rozwinęły się możliwości diagnostyczne i interfejsowe maszyny za pomocą paneli HMI. Te urządzenia umożliwiły wyświetlanie informacji otrzymanych ze sterownika PLC za pomocą protokołu komunikacyjnego. Na początku tylko w formie tekstowej ale wraz z rozwojem technologii również w formie graficznej. Równolegle do sterowników rozwijały się również roboty przemysłowe, które zastąpiły człowieka w prostszych i żmudnych czynnościach. PLC mają możliwość wymiany danych z robotami i te systemy mogą ze sobą współdziałać. Sterowniki stają się coraz mniejsze, a ich możliwości coraz bardziej zaawansowane np. integracja z systemami wizyjnymi. Mogą one wykorzystywać nowe metody komunikacji co umożliwia zintegrowanie sterowania z takimi systemami jak SCADA, MES i ERP.
Popularyzacja PLC i wprowadzenie ich do fabryk zapoczątkowało trzecią rewolucją przemysłową czyli automatyzacje. Sterowniki umożliwiły łatwą edycje programu i pomoc w diagnostyce usterek pojawiających się podczas pracy maszyny. Szafy elektryczne mogły stać się mniejsze, ponieważ nie musiały już posiadać tak dużej ilości przekaźników i styczników. Sterowniki PLC zmniejszyły koszty wytwarzania maszyn i czas ich wdrożenia w fabryce, a co za tym idzie zmniejszyły koszty produkcji.
Miejsce sterowników PLC w piramidzie automatyzacji przemysłu
PLC znajdują się na niższym poziomie piramidy automatyzacji odpowiedzialnym za sterowaniem maszynami. Zbierają one dane z czujników i względem tego w zaprogramowany sposób sterują maszyną. Komunikują się z systemami SCADA i HMI w celu wizualizacji procesów produkcyjnych i ułatwieniu interfejsu między człowiekiem, a maszyną.
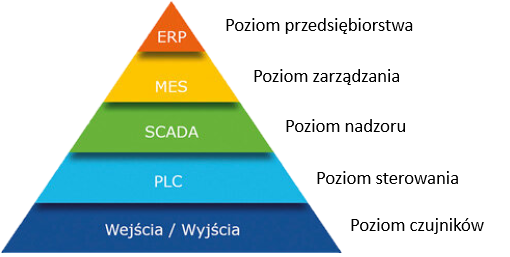
Prawie we wszystkich maszynach w przemyśle spotyka się PLC czasem nawet może być kilka w jednej, odpowiedzialnych za różne sekcje. Sterowniki PLC cechuje niezawodność i wytrzymałość pozwalająca na pracę w przemysłowych warunkach. W zależności od charakteru fabryki maszyny potrafią być włączone 24h na dobę i to właśnie PLC jest odpowiedzialne za to że wszystko działa prawidłowo. W fabrykach nadal można spotkać sterowniki, które mają ponad 20-30 lat i ciągle spełniają swoją funkcje.
Na przestrzeni lat zwiększyły się możliwości programowania, komunikacji, zmniejszenie czasu cyklu i środowiska programistyczne niejednokrotnie ewoluowały. Nowoczesne sterowniki PLC są przystosowywane do komunikacji z systemami IT zgodnie z myślą przemysłu 4.0. Ich zastosowanie jest bardzo uniwersalne od prostego sterowania przenośnikiem po sterowanie całymi procesami technologicznymi. Posiadają możliwość komunikacji poprzez protokoły bardziej kojarzone ze światem IT jak OPC UA i MQTT. Zbierają dane z czujników, których jest możliwość wysłania nawet do chmury.
Budowa sterowników PLC
Wyróżnia się kilka komponentów z których może być zbudowany sterownik PLC, w zależności od wymogów aplikacji stosuje się odpowiedni typ i ilość. Prócz jednostki centralnej występują moduły rozszerzeń, które różnią się funkcjonalnością:
- CPU - Jednostka centralna sterownika. Tam wykonywany jest program i cała logika jest w nim zawarta. Najczęściej ten moduł już posiada wbudowaną możliwość komunikacji z PC w celu programowania, oraz komunikacji z innymi urządzeniami wykorzystującymi ten sam zaimplementowany protokół komunikacyjny.
- Wejścia cyfrowe - odbierają one sygnały z czujników , przycisków, krańcówki itp. Różnią się w zależności od napięcia odbieranego sygnału oraz ilości wejść w danym module. Odbierają stan wysokiego (1) lub niskiego napięcia (0).
- Wyjścia cyfrowe - wysyłają sygnał sterujący typu włącz/ wyłącz do urządzeń które chcemy załączać np. lampka, silnik, pompa, grzałka itp. Moduły mogą posiadać różną ilość wyjść oraz typ tranzystorowe lub przekaźnikowe. Wyjście tranzystorowe najczęściej wysyła sygnał 24 V DC i posiada niską obciążalność prądową ok. 0,5 A, ale takich wyjść może się znaleźć duża ilość w jednym module. Wyjścia przekaźnikowe mogą sterować większym napięcie oraz posiadają większą obciążalność do nawet 6A, jednak ich ilość w module jest dosyć niska.
- Wejścia analogowe - odbierają sygnały analogowe z czujników pomiarowych, typu temperatura, ciśnienie oraz pomiary typu waga itp. Posiadają wbudowane przetworniki analogowo-cyfrowe pozwalające na konwersje sygnału w sposób zrozumiały dla CPU. Różni się on w zależności od rozdzielczości wejścia (11 bit, 12 bit ...). Mogą odbierać sygnały w różnych formatach najczęściej w standardzie 0-10V, -10-10V, 0-20mA, 4-20mA w zależności od konfiguracji danego wejścia.
- Wyjścia analogowe - wysyłają sygnały analogowe do, które można sterować płynnie np. prędkość obrotu silnika, częściowe otwarcie zaworu. Posiadają przetworniki cyfrowo-analogowe i mogą wysyłać sygnały napięciowe (0-10V, -10-10V) i prądowe (0-20mA, 4-20mA).
- Moduł zasilania - dostarcza on potrzebne zasilania do wszystkich modułów, w zależność od budowy może to robić przez płytę bazową, magistralę zasilającą lub przez przewody.
- Moduł komunikacyjny - pozwala na komunikacje z innymi urządzeniami i rozszerza obsługę o inne protokoły.
- Moduł specjalistyczny - mogą to być np. moduł ruchu pozwalająca na dokładne sterowanie serwonapędami, moduł szybkich liczników pozwalające na wykrywanie impulsów sygnałów o wysokiej częstotliwości.
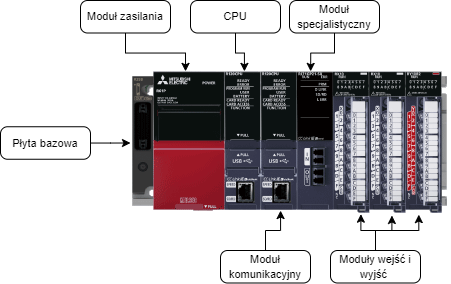
Grupy sterowników PLC
Sterowniki można podzielić na grupy w zależności od ich budowy:
- kompaktowy: CPU posiada już wbudowane wejścia, wyjścia dzięki czemu kupując jedno urządzenie już można stworzyć system sterowania. Ten rodzaj PLC jest tańszy ale możliwość rozbudowania o kolejne wejścia/ wyjścia itd. jest dosyć ograniczona. Jego komponenty można umieszczać bezpośrednio na szynie DIN w szafie elektrycznej. Zwykle są one używane do mniejszych i średnich aplikacji i maszyn.
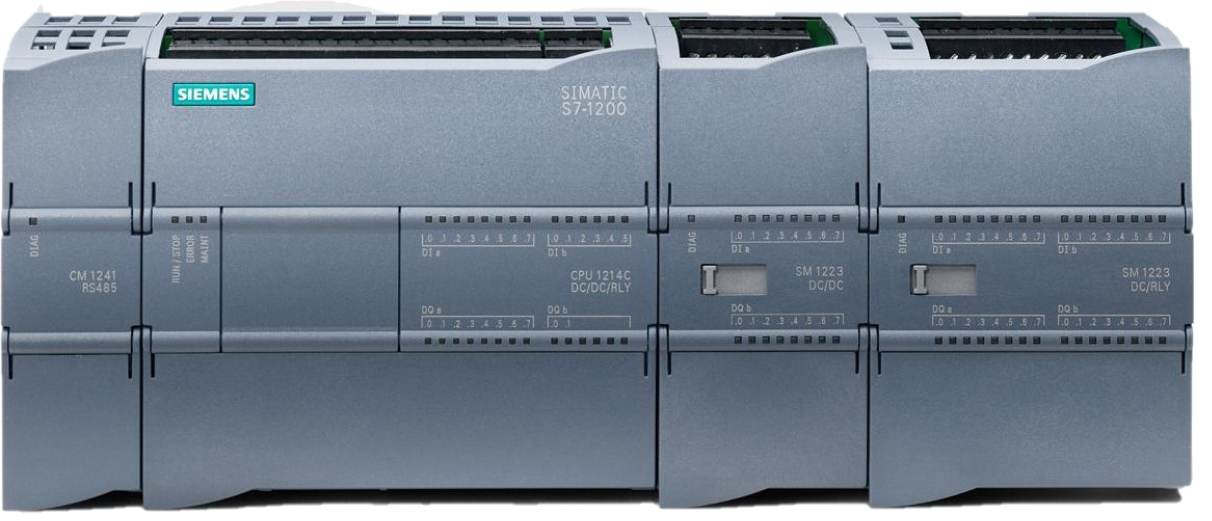
- modułowy: CPU posiada wydajniejszy procesor, więcej pamięci niż wersja kompaktowa. Jest możliwość dużej rozbudowy sterownika o kolejne moduły. Każdy z tych modułów jest od siebie niezależny. Zwykle do sterownika PLC należy dokupić płytę bazową na której zostanie umieszczony wraz z modułami. Najczęściej są stosowane do średnich i dużych systemów sterowania.
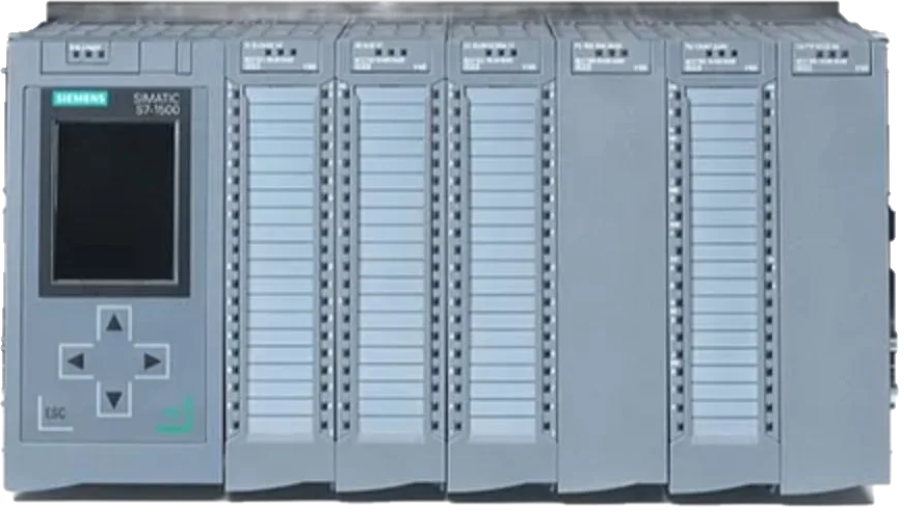
Cykl pracy sterownika PLC
Sterowniki PLC działają w zamkniętym cyklu programowym dzięki czemu mogą na bieżąco odczytywać stan wejść sterownika w celu zaktualizowania wyjść. Czas cyklu jest zależny od stopnia zaawansowania wykonywanego programu oraz od mocy obliczeniowej danego sterownika. Zwykle jest to w granicy od kilku do kilkudziesięciu milisekund.
Niektóre ze sterowników posiadają możliwość przypisania części funkcji programu do danego czasu cyklu skanowania (np. 10ms, 50ms). Umożliwia to optymalne wykorzystanie CPU i skupienie mocy obliczeniowej na bardziej wymagających aspektach. Przykładowo temperaturę w pokoju nie musimy odczytywać co 100ms, ponieważ ona nie jest aż tak często zmienna. Natomiast gdy jest potrzeba odczytywania dokładnej pozycji silnika należy to robić jak najczęściej nawet co 5ms.
Czynności wykonywane przez sterownik:
- Inicjalizacja sterownika PLC - Sprawdzenie poprawności konfiguracji sterownika, odczyt statusów wykorzystanych modułów. Po pozytywnej inicjalizacji przejście sterownika z trybu STOP do trybu RUN.
- Rozpoczęcie cyklu - Start cyklu pracy sterownika.
- Odczyt sygnałów wejściowych - Sprawdzenie stanu sygnałów na modułach wejściowych i przekazanie ich wartości do CPU.
- Wykonanie programu - Implementacja wartości sygnałów wejściowych do programu logicznego i wykonywanie go linijka po linijce.
- Aktualizacja wyjść - Na podstawie wykonanego programu, aktualizowany jest stan wyjść sterownika PLC.
- Obsługa komunikacji - Jeżeli inne urządzenia w sieci komunikacyjnej są połączone ze sterownikiem, następuje wymiana danych.
- Autodiagnostyka - Sprawdzenie błędów i statusów sterownika. W przypadku wykrycia krytycznego błędu cykl pracy sterownika PLC jest przerywany, zmiana z trybu RUN na tryb STOP
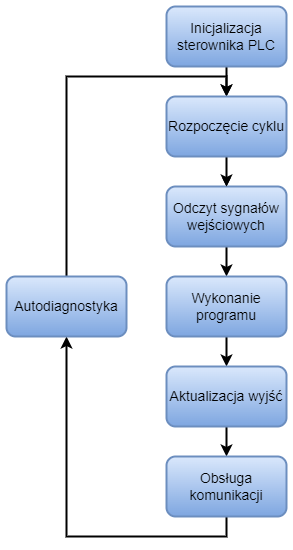
Programowanie sterowników PLC
Środowiska programowania PLC
Programowanie sterownika PLC odbywa się za pomocą komputera poprzez dedykowane środowisko programistyczne. Każdy z producentów posiada środowisko dla swojej serii sterowników np.:
- Siemens - TIA Portal,
- Mitsubishi - GxWorks,
- Omron - Sysmac Studio,
- Wago - e!COCKPIT,
- Allen Bradley - Studio 5000
Istnieje również środowisko Codesys, które umożliwia programowanie różnych wspieranych sterowników PLC firm m.in.: Eaton, Lenze, Schneider, Astraada One. W zależności od podejścia producenta niektóre z tych środowisk mogą być płatne.
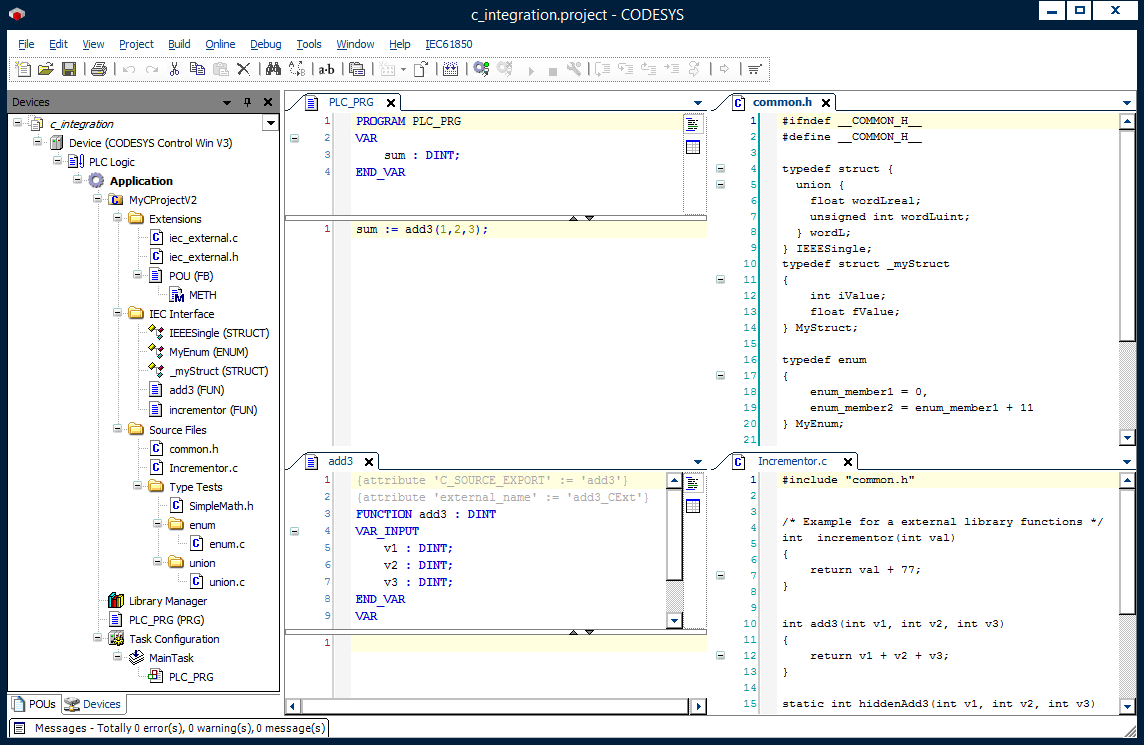
CODESYS - środowisko programowania sterowników PLC
Sposoby wgrywania programu do PLC
W dzisiejszych czasach podłączenie między komputerem a PLC odbywa się za pomocą Ethernet lub za pomocą przewodu USB. Dzięki wykorzystaniu Ethernetu nie trzeba być komputerem podpiętym bezpośrednio do sterownika. Wystarczy być podłączonym do switcha, który jest w tej samej sieci. W komputerze należy ustawić statyczny wolny adres IP w tej samej sieci, w której znajduje się sterownik PLC. Sprawdzenie ustabilizowania komunikacji można sprawdzić za pomocą komendy ping <adres IP PLC> w konsoli lub za pomocą dedykowanego środowiska programistycznego. Niektóre nowoczesne środowiska programistyczne potrafią mostkować połączenie między sieciami jednak ustawienie statycznego IP w PC jest przyjmowane jako dobra praktyka.
Istnieje możliwość podłączenia się do sterownika za pomocą sieci WIFI co może okazać się pomocne podczas testowania logiki działania maszyny i podglądzie zmiennych. Jednak nie jest zalecane wtedy wgrywanie istotnych zmian szczególnie przy pracującej maszynie, ponieważ w fabryce mogą pojawiać się zakłócenia, które mogą przerwać połączenie. Przerwanie połączenia między PLC, a komputerem podczas wgrywania programu może prowadzić do błędu i zatrzymania sterownika.
Podłączenie przez Ethernet umożliwia również zdalne programowanie sterownika PLC za pomocą tunelu VPN, zdalna aktualizacja programu pomaga szybciej wprowadzać zmiany w razie ewentualnych awarii lub dodania funkcjonalności.
Przy podłączeniu komputera z PLC za pomocą przewodu USB należy z menedżera urządzeń odczytać numer portu COM i wprowadzić ten sam numer w środowisku programistycznym danego sterownika.
Dawniej do podłączenia komputera z PLC służyły dedykowane przewody z portem szeregowym RS232/485, lecz każdy producent projektował go w różnej formie i stwarzało to dodatkowe problemy w trakcie serwisu. Sprawdzenie komunikacji należy rozpocząć od określenia poprawności parametrów komunikacji w komputerze i w sterowniku, muszą być takie same, a są to m.in.: prędkości transmisji, bitu parzystości, bitu stopu.
Po poprawnym skonfigurowaniu i sprawdzeniu połączenia istnieje możliwość wgrywania programu napisanego w dedykowanym środowisku do sterownika PLC.
Języki programowania sterowników PLC
Norma IEC 61131-3 ustandaryzowała języki programowania sterowników PLC. Zdefiniowane zostało w jaki sposób może być budowany program w danym języku. Dzięki unormowaniu inżynierzy nie muszą uczyć się od nowa programowania gdy wykorzystywany jest sterownik innego producenta. Zdefiniowano również typy danych jakie sterownik powinien mieć możliwość obsługi. Języki można podzielić na graficzne ( LAD, FBD, SFC) i tekstowe (ST, IL).
LD (Schemat drabinkowy)
Język ten powstał jako jeden z pierwszych języków programowania PLC, jest odzwierciedleniem schematu elektrycznego do języka programowania. Jego podstawowymi elementami są styki (NO, NC) odzwierciedlające styki przekaźnika i cewki odzwierciedlające cewkę przekaźnika i załączenie urządzenia.
Jest to najpopularniejszy język programowania szczególnie w połączeniu z FBD, bardzo łatwy do diagnostyki logiki działania. Najczęściej wykorzystuje się do zapisywania logiki maszyny, obsługi alarmów i pisania funkcji.
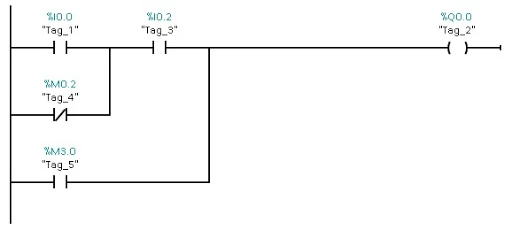
FBD (Funkcjonalny schemat blokowy)
Język ten odpowiada przepływowi sygnałów obwodów logicznych. Program buduje się na zasadzie podłączania bloczków funkcyjnych i bramek logicznych.
Często jest możliwość mieszania tego języka z językiem LD. FBD również jest stosowany to programowania procesów technologicznych.
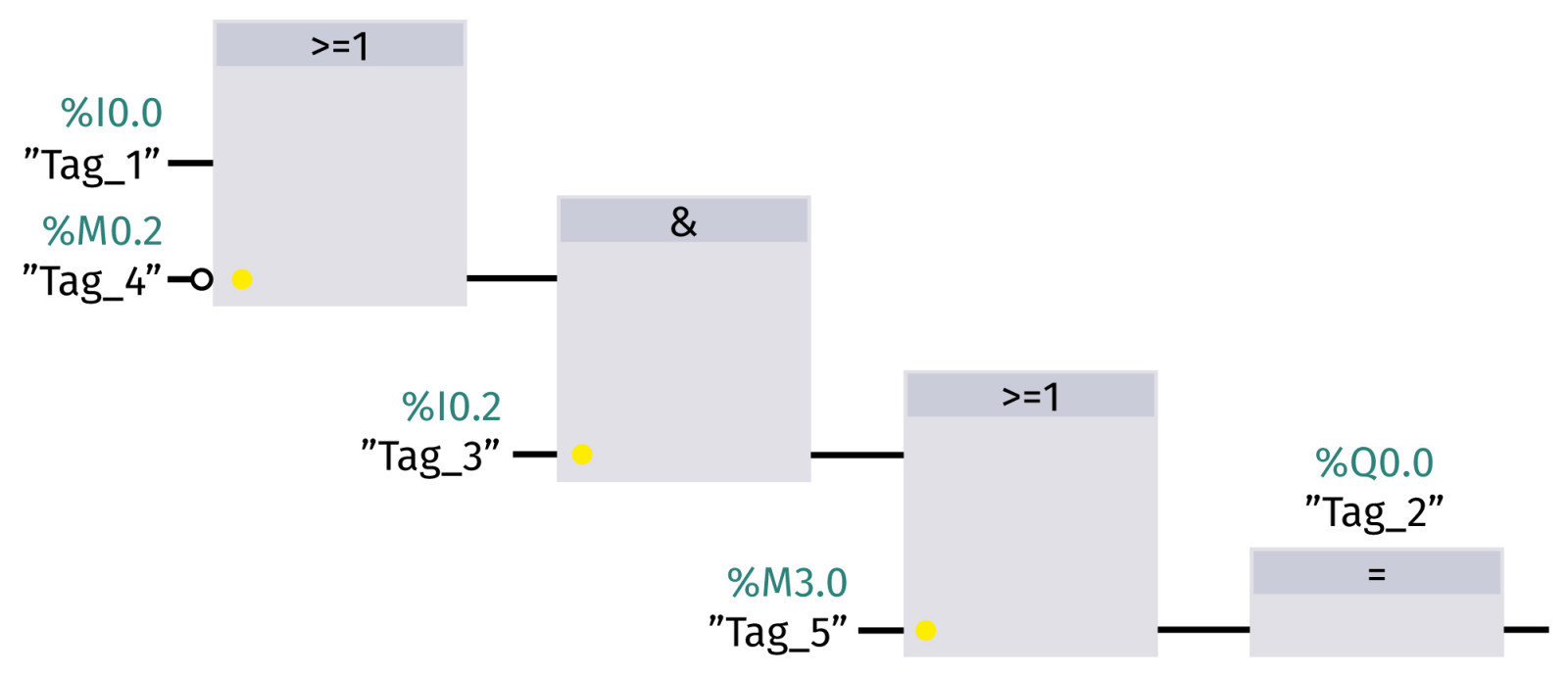
SFC (Sekwencyjny diagram funkcjonalny)
Wzorowany na diagramie przepływu, można zapisywać w nim sekwencje działania danej maszyny. Język składa się z kroków i tranzycji (warunku) połączonych ze sobą w diagramie. W krokach zapisuje się akcje czyli funkcje i zmienne które mają się wykonać, natomiast w tranzycji zawarte są warunki jakie muszą zostać spełnione aby przejść do kolejnego kroku.
Zwykle ten język stosuje się jako nadrzędny kontrolujący sekwencje pracy maszyny.
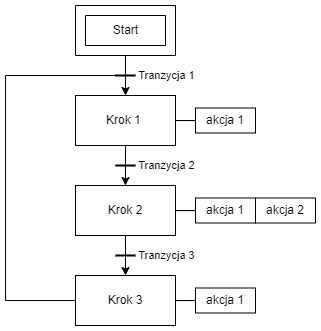
ST (Tekst strukturalny)
Język składający się z poleceń tekstowych bazujący na językach programowania PASCAL i C. W porównaniu do innych języków bardzo dobrze sprawdza się w obliczeniach i pracy na tablicach.
W związku z łączeniem świata IT i OT ten język zyskuje na popularności również do zapisywania funkcji logicznych.
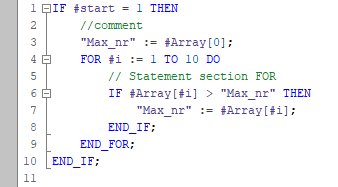
IL (Lista instrukcji)
Zapisywanie logiki w sposób tekstowy, w każdej linijce znajduje się osobno instrukcja do wykonania. Bazuje na języku typu asembler, więc działa na zasadzie wykonywania instrukcji ze zmiennymi na stosie.
Kiedyś bardzo popularny język przed unormowanie ST natomiast teraz rzadko spotykany w nowych systemach sterowania.
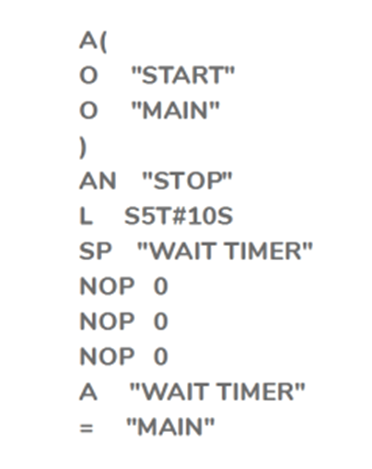
W jaki sposób programować?
Programowanie sterowników PLC różni się w zależności od oprogramowania jakie jest używane. Jednak w każdym z nich można wyróżnić takie same kroki tj.:
- Tworzenie projektu wraz z wybraną wersją CPU
- Konfiguracja hardware
- Adresacja zmiennych wejściowych i wyjściowych w modułach sterownika
- Tworzenie zmiennych
- Pisanie programu wraz z tworzeniem funkcji
- Podłączenie się do sterownika PLC
- Kompilacja i wgranie programu do sterownika
- Włączenie wykonywania programu PLC (przejście z trybu STOP do RUN)
Typy danych w sterownikach PLC
W sterownikach PLC każda zmienna zapisywana jest w rejestrze pamięci dlatego każda z nich musi mieć określony typ. W zależności w jaki sposób chcemy wykorzystywać zmienną i jakie informacje ma przechowywać należy zdefiniować jej typ.
Typ | Rozmiar | Format | Opis |
---|---|---|---|
BOOL | 1 bit | 0 lub 1 | status pojedynczego sygnału |
BYTE | 8 bitów | 00010101 | zestaw 8 sygnałów |
WORD | 2 bajty | 16#0 | słowo bitowe |
INT | 2 bajty | 21434 | liczba całkowita |
REAL | 4 bajty | 3123.31 | liczba zmiennoprzecinkowa |
CHAR | 1 bajt | “ABC” | litera |
STRING | zmienny | “Sterownik PLC” | zdanie |
Mapowanie zmiennych
W zależności od przeznaczenia zmienne przechowywane są w różnej lokalizacji. To od programisty zależy czy dana zmienna będzie zaadresowana automatycznie czy poprzez narzucone adresy rejestru. Składają się z litery jako przedrostka i liczby odnoszącej się do kolejnego numeru adresu lub do konkretnego fizycznego wejścia/ wyjścia.
Najczęściej spotykane oznaczenia to I dla wejścia, Q dla wyjścia, M dla flag. Do danej zmiennej można odnosić się albo po jej nazwie albo po przydzielonym adresie. Podczas konfiguracji modułów wejść i wyjść dodaje się tagi odnoszące się do danego wejścia/wyjścia poprzez nadanie im odpowiedniego adresu.
W programie nie można powtórzyć tego samego adresu dla dwóch różnych zmiennych w obrębie jednego PLC. Sterowniki posiadają ograniczoną ilość zmiennych, które jest zdefiniowana w dokumentacji ile jakiego typu zmiennych można wykorzystać.
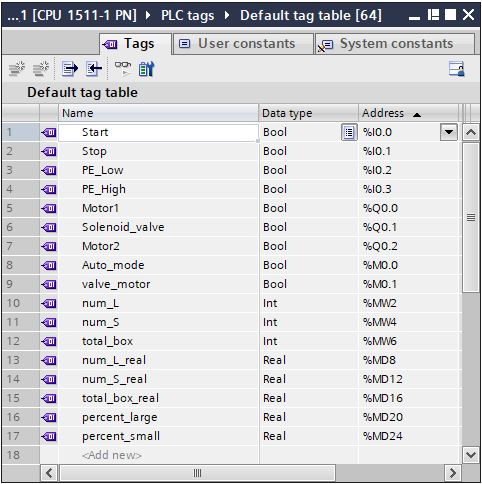
Pisanie programu dla PLC - dobre praktyki
W związku z tym, że maszyny w przemyśle mają być niezawodne i pracować wiele lat warto pisać program w taki sposób aby był zrozumiały i przejrzysty. W jednym programie PLC mogą znajdować się fragmenty kodu napisane w różnych językach, które można wykonywać na zasadzie wywołania danej funkcji. Każdy z języków ma swoje mocniejsze i słabsze strony. Warto je wykorzystywać zależnie od fragmentu logiki jaki chcemy wykonać. W niektórych środowiskach programistycznych języki FBD i LD mogą być wywoływane w jednym fragmencie kodu co umożliwia dodanie bloków funkcyjnych i ich wywołanie za pomocą logiki zapisanej w LD.
- LD i FBD: logika pracy, alarmy, wywołanie i zapis funkcji, komunikacja
- ST: wykonywanie obliczeń, sekwencja pracy, praca na tablicach, prosta logika
- SFC: nadrzędna sekwencja pracy
Warto trzymać się kilku praktyk w celu przejrzystości kodu i łatwej edycji nawet po kilku latach:
- Nazywanie zmiennych zgodnie z ich pełniącą funkcją oraz zachowując nazwę urządzenia zgodną z dokumentacją elektryczną np.: Motor1_start, S1_auto.
- Dzielenie programu na sekcje w zależności od ich wykorzystania.
- Tworzenie funkcji w celu zapisania powtarzających się rozwiązań wraz z określeniem wewnętrznych zmiennych wejściowych i wyjściowych danej funkcji. Pozwala to wywołać daną funkcje kilkukrotnie i zmiana logiki jest możliwa w prosty sposób np.: funkcja "Przenośnik".
- Zakładanie rezerwowej ilości zmiennych, szczególnie dla alarmów. Do danej maszyny mogą dochodzić nowe funkcjonalności i rozwiązania, a zapasowe zmienne mogą zostać szybko wykorzystane.
- Zapisywanie w różnych tabelach zmienne w zależności do jakiego urządzenia są wysyłane lub za co odpowiadają np.: Alarmy, HMI, Wejścia, Wyjścia.
- Dodawanie daty zapisu do kolejnych wersji programu.
- Przed aktualizacją programu w PLC należy sprawdzić i porównać posiadaną wersję z tą wgraną na sterownik. Należy mieć świadomość wprowadzanych zmian, ponieważ może to doprowadzić do awarii maszyny.
Komunikacja
Sterowniki PLC posiadają możliwość komunikacji wykorzystując protokoły komunikacyjne. Wykorzystywane jest to do wymiany danych m.in.: panelami HMI, wyspami wejść/wyjść, falownikami, systemami SCADA, urządzeniami sterującymi napędem, czujnikami. Wymiana danych polega na zasadzie udostępniania wartości rejestru i dane urządzenie musi obsługiwać ten sam protokół komunikacyjny. W konfiguracji hardware w środowisku programistycznym należy wcześniej zdefiniować i połączyć urządzenia w jedną sieć. Podczas programowania komunikacji często korzysta się z dodatkowych bloków funkcyjnych przygotowanych przez producenta, szczególnie gdy chcemy się połączyć z urządzeniami typu sterowania napędem. Producent danego urządzenia klienckiego określa jakie zmienne i na jakich adresach mogą służyć do odczytu lub zapisu. Przykładowo chcąc wyświetlić status pracy danego silnika należy przypisać tą zmienną do adresu np.: %I3.2 ten sam adres należy wprowadzić w panelu HMI i podpiąć go do lampki, która się będzie podświetlała gdy sterownik wykryje, że silnik pracuje.
Dobór sterownika PLC
W przemyśle bardzo ważna jest niezawodność systemu sterowania i możliwość jej modyfikacji. Dlatego dobór sterownika jest kluczowym aspektem podczas projektowania maszyny. Podczas projektowania systemu sterowania należy zwrócić uwagę na kilka aspektów, które mogą decydować o tym jaki rodzaj sterownika zostanie wykorzystany.
- Określenie wielkości aplikacji czy jest to duży czy mały system sterowania. Sterowniki różnią się mocą obliczeniową, która definiuje wielkość programu. Jeśli dany sterownik ma możliwość obsługi maksymalnie 8 modułów i z listy systemu sterowania też nam tyle wychodzi. To lepiej zdecydować się na większy sterownik, który zawsze będzie można rozbudować w przyszłości
- Sporządzenie listy wymaganych modułów poprzez obliczenie i określenie rodzaju wejść i wyjść jakie znajdują się w danym systemie. Warto dobrać tak moduły aby pozostawał zapas wolnych wejść i wyjść na modułach w celu przyszłej modernizacji, można dobrać aby zapasu było ok. 10%. Należy też określić czy są potrzebne dodatkowe moduły komunikacyjne lub inne specjalistyczne np. do sterowania napędami.
- Standaryzacja sterowników PLC w obrębie danej fabryki może być wymóg stosowania sterowników tylko jednego producenta. Ułatwia to takim działom jak utrzymanie ruchu serwis maszyny oraz umożliwia łatwiejszy dostęp do części zamiennych.
- Wymiana danych z innymi systemami nadrzędnymi, które mogą zbierać dane z maszyn. Sterownik PLC powinien mieć możliwości obsługi tego samego protokołu, który już jest zaimplementowany na fabryce. Osiąga się to poprzez wbudowane protokoły komunikacyjne w CPU albo poprzez dodatkowe moduły komunikacyjne.
- Doświadczenie i posiadane środowisko programistyczne sterowników PLC. Niektóre z oprogramowań mogą być płatne, więc warto wybrać sterownik PLC do którego już posiadamy środowisko. Doświadczenie w programowaniu danego sterownika również jest ważne i ma bardzo duże znaczenie szczególnie przy większych aplikacjach.
- Dostępność i cena może się różnić wraz z upływem czasu. Warto dobrać tak sterownik żeby spełniał swoją funkcję, ale też bez potrzeby wydawania dodatkowych pieniędzy.
- Gotowe rozwiązania i wsparcie z innymi urządzeniami. Producenci różnego typu urządzeń mogą ze sobą współpracować dostarczając gotowe rozwiązania dla obsługi danej funkcjonalności.
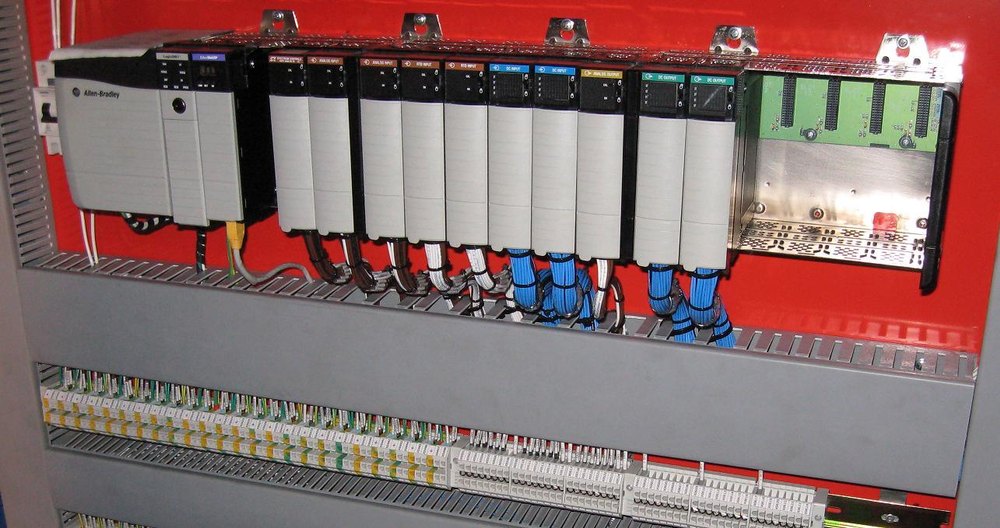
Zastosowanie
Sterowniki PLC najczęściej kojarzone są z automatyką przemysłową jako "mózgi" systemów sterowania znajdujących się maszyn na fabryce. Dzięki ich stosowaniu można przyśpieszyć i zoptymalizować produkcje, a co za tym idzie zmniejszyć koszt wytwarzanego produktu. Programowalne sterowniki logiczne posiadają same zalety: wytrzymałość, stabilność, standaryzacja, wysokie możliwości diagnostyczne, łatwa edycja programu i możliwość jego powielania. Jedyną ich wadą może okazać się cena jednak można to zniwelować odpowiednim doborem i porównując to do układów stycznikowo przekaźnikowych to i tak wychodzi tańszy sterownik. PLC występują w każdej gałęzi przemysłu mogą się różnić w zależności od ich przeznaczenia:
- Automatyka przemysłowa - Systemy sterowania w przemyśle oparte są głównie na wykorzystaniu sterowników PLC.
- Automatyka budynkowa - Sterowniki tego typu będą posiadały wsparcie protokołów komunikacyjnych takich jak KNX i DALI. Zwykle posiadają wtedy mniejszą budowę i są odpowiedzialne m.in.: za sterowanie oświetleniem, systemy HVAC, systemy kontroli dostępu.
- Przejazdy kolejowe - Sterownik jest odpowiedzialny za sygnalizacje i szlabany na przejeździe. Cechują się sygnałami spełniającymi normy bezpieczeństwa, oraz posiadają wysoki standard niezawodności elektrycznej i poziom nienaruszalności bezpieczeństwa SIL.
- Sygnalizacja świetlna - Sterowanie sygnalizacji świetlnej na skrzyżowaniach, odporność na warunki atmosferyczne.
Sterowniki PLC nie tylko mogą służyć do wykonywania logiki działania ale również do otrzymywania danych z różnego rodzaju sygnałów z czujników, obliczania czasu pracy maszyny i ilości wyprodukowanego produktu, obliczanie zużycia subproduktów itd. Nowoczesne PLC mają nawet możliwości podłączenia się do bazy danych więc udostępnianie danych produkcyjnych do systemów nadrzędnych również nie stanowi problemu.