Jak cyfryzacja i automatyzacja poprawia efektywność produkcji w firmie z branży meblarskiej
Jak firma programistyczna ImpiCode wspiera producentów mebli na każdym etapie produkcji?
Proces produkcji mebli krok po kroku
Etap 1: Cięcie płyt
Zazwyczaj pierwszym krokiem w produkcji mebli jest rozkrój płyt na odpowiednie elementy. W zależności od rozmiaru zakładu i poziomu zautomatyzowania, można spotkać się z w pełni zautomatyzowaną linią pilarek, maszyną CNC lub dedykowanym centrum cięcia płyt. W przypadku centrum cięcia maszyna wykonuje szybkie i bardzo dokładne cięcia, jednak niezbędny jest operator do przygotowania płyt do cięcia oraz ich odbioru.
Pilarka do cięć płyt meblowych HOLZ-HER CUT 6120
Strzałki lasera pokazują jak przesunąć/obrócić płytę
Pilarka do cięć płyt meblowych Schelling FH 6
Możliwe funkcjonalności do wdrożenia:
- Integracja z oprogramowaniem CAD/CAM w celu odczytu projektu przez maszynę.
- Etykietowanie detali w celu pełnej kontroli procesu.
- Monitorowanie i zliczanie wyprodukowanych detali.
- Wsparcie składowania wyciętych płyt.
- Wyświetlanie instrukcji dla operatora: ekran, projekcja laserowa strzałek na detalu.
Korzyści z cyfryzacji:
- Szybsze przezbrajanie maszyn dzięki automatycznemu przesyłaniu projektów.
- Zmniejszenie ilości zmarnowanego surowca dzięki szczegółowym instrukcjom dla operatorów.
- Monitorowanie w czasie rzeczywistym zapobiega przestojom i umożliwia śledzenie postępu realizacji planu.
- Ułatwienie harmonogramowania serwisów poprzez liczniki roboczogodzin, czasu cięcia oraz przeciętych metrów.
Etap 2: Oklejanie krawędzi
Po pocięciu płyt następuje faza oklejania krawędzi. Choć czynność ta wydaje się prosta, wymaga dużej precyzji i ostrożności, ponieważ jest kluczowa dla wykończenia.
Oklejarki, oprócz taśm transportowych, dozowników kleju i docisków obrzeży, posiadają różne agregaty obróbcze dostosowane do wymaganego oklejania. Jednym z popularniejszych jest frez wstępny, eliminujący niedokładności powstałe podczas cięcia płyt. W przypadku grubszych oklein zastosowanie mają również agregaty zaokrąglające, nabłyszające i polerujące obrzeże.
Okleiniarka krawędzi SCM Holzkraft Minimax ME 25S
Okleiniarka krawędzi BRANDT KDF 650
Okleiniarka krawędzi BRANDT Highflex 1220
Możliwe funkcjonalności do wdrożenia:
- Odczytywanie z etykiety informacji o produkcie.
- Informowanie operatora o elementach, które będą oklejane.
- Prezentowanie operatorowi, jaką okleinę należy przygotować, gdzie ją znaleźć oraz jak skonfigurować maszynę.
- Obliczanie ilości potrzebnych półproduktów oraz informowanie o konieczności ich przygotowania.
- Systemy wizyjne do kontroli jakości okleinowania.
- Monitorowanie w czasie rzeczywistym liczby obrobionych detali.
- Możliwość kontrolowania temperatury: kleju, otoczenia, okleiny.
Korzyści z cyfryzacji:
- Natychmiastowe wykrywanie defektów wizualnych okleiny.
- Monitorowanie temperatury zapobiega nietrwałemu oklejaniu elementów.
- Ciągłe monitorowanie zapobiega przestojom oraz ułatwia osiągnięcie zamierzonego planu.
- Skrócenie czasu przezbrajania maszyny.
Etap 3: Wiercenie
Mając już pocięte i oklejone elementy, przechodzimy do wiercenia otworów na kołki, śruby i zawiasy. Czyli niezbędnych elementów montażowych, dzięki którym pojedyncze płyty przybiorą kształt mebli. Otwory te mogą być nawiercane z obu stron detalu, a także na jego krawędziach.
Do tego zadania półprodukty mogą być obrabiane w różnych maszynach – na przykład inna maszyna będzie używana do nawiercania otworów na krawędziach, a inna do otworów na powierzchniach. Czasami konieczne jest kilkukrotne użycie tej samej maszyny, przy odpowiednim obracaniu elementu przez operatora.
Niezwykle ważnym aspektem jest pilnowanie, czy maszyna CNC ma właściwy program dla danego elementu oraz czy operator umieścił element w odpowiedni sposób. Dlatego kontrolowanie, czy powstałe elementy są zgodne z projektem, jest kluczowe.
Wiertarka CNC Busellato JET SMART
Centrum CNC Cormak HK 52
Wiertarka CNC Masterwood TF600S
Możliwe funkcjonalności do wdrożenia:
- System wizyjny rozpoznający rodzaj elementu i ładujący odpowiedni program.
- System wizyjny oceniający, czy detal ma nawierty zgodne z planem i czy nie doszło do uszkodzenia elementu.
- System wizyjny oceniający jakość nawierceń.
- Obliczanie i predykcja zużywalności osprzętu oraz pilnowanie harmonogramu wymian.
- Monitorowanie w czasie rzeczywistym przetworzonych detali.
Korzyści z cyfryzacji:
- Mniej zmarnowanych detali dzięki szybkiej diagnozie błędów.
- Minimalizacja błędnie wykonanych detali.
- Zwiększenie wydajności dzięki szybszej pracy operatora (automatyczne wskazywanie, co ma robić).
Składowanie i transport między etapami
Omówiliśmy trzy pierwsze etapy produkcyjne w stolarni: cięcie płyt, oklejanie krawędzi i nawiercanie otworów. W zależności od rodzaju mebli, proces produkcji może obejmować kolejne etapy, takie jak montaż dodatkowych elementów, obicia i oszycia, czy składanie wcześniej wyprodukowanych komponentów w gotowe półprodukty i produkty. Niezależnie od specyfiki produkcji, kluczową rolę odgrywa składowanie detali i ich transport między poszczególnymi maszynami.
W zależności od wielkości zakładu, zastosowanych maszyn, produkowanych elementów i dostępnej przestrzeni, systemy transportowe mogą się znacznie różnić. Do najpopularniejszych należą:
- Taśmociągi: Automatyczne przenośniki taśmowe, które szybko i sprawnie transportują elementy między stanowiskami.
- Systemy rolkowe: Prócz ułatwiania transportu mogą pełnić rolę bufora między różnymi maszynami.
- Podajniki na ramionach i suwnicach: Idealne do przenoszenia dużych, ciężkich lub niewygodnych w transporcie elementów.
- Transport na paletach/platformach: Zarówno ręcznie przez pracowników, jak i automatycznie przez odpowiednie roboty AGV (Automated Guided Vehicles).
Podstawowym wyzwaniem tych systemów jest zapewnienie sprawnego transportu półproduktów, aby uniknąć zatorów w produkcji. Często również realizują funkcję bufora półproduktów, które przydadzą się w późniejszym etapie produkcji. Wszystko to musi być realizowane z dużą elastycznością, umożliwiającą szybkie zmiany w produkcji i adaptację używanych maszyn w zależności od aktualnie produkowanych mebli.
Zrobotyzowany transport palet
System składowania płyt IMA Schelling Board
Robot KUKA zdejmuje detale z podajnika rolkowego
Możliwe funkcjonalności do wdrożenia:
- Automatyczne przygotowywanie i odbieranie płyt.
- Śledzenie lokalizacji detali za pomocą kodów kreskowych/QR, systemów wizyjnych lub czytników RFID.
- Grupowanie informacji o wyprodukowanych detalach z różnych maszyn i ostrzeganie o możliwych zatorach z powodu braku półproduktów lub wolnego miejsca do składowania przy maszynie.
- Wykrywanie błędów w transporcie detali takich jak zastawiona droga dla robota transportowego lub zablokowany taśmociąg.
Korzyści z cyfryzacji:
- Zwiększenie ogólnej wydajności stolarni poprzez wyeliminowanie zatorów spowodowanych brakiem elementów.
- Zmniejszenie ilości pracy ręcznej na rzecz automatycznego systemu składowania i przekazywania elementów do maszyn obróbczych.
- Bieżące informacje o procencie zrealizowanego planu na dany dzień z dokładną estymacją końcowego wyniku.
- Zmniejszenie ilości zmarnowanego materiału dzięki wyeliminowaniu pomyłek w dostarczaniu detali.
Etap 4: Konfekcjonowanie i pakowanie
Dotarliśmy do etapu, w którym należy skompletować odpowiednie elementy w paczkę. W zależności od produktu lub wymagań klienta proces ten różni się, np. klient może wymagać ofoliowania niektórych elementów, takich jak półki regału. Jednak co do zasady polega on na umieszczeniu w kartonie odpowiednio przygotowanych płyt i półproduktów, woreczków z drobnymi elementami montażowymi oraz instrukcji do montażu. Często wymagane jest również zastosowanie odpowiednich dystansów i wypełniaczy, które uniemożliwiają poruszanie się elementów wewnątrz zapakowanego kartonu.
W zależności od charakteru pakowanych produktów, można usprawnić pracę poprzez zastosowanie kartoniarek, które automatyzują proces składania kartonów. Jest to szczególnie przydatne w przypadku większych elementów, gdzie ręczne składanie kartonów może być czasochłonne i męczące. Pomimo pewnej automatyzacji, często niezbędna jest manualna praca pracowników, którzy odpowiednio ułożą wszystkie elementy i przygotują niezbędną ilość detali.
Ważne jest zapewnienie ergonomicznych stanowisk do pakowania oraz łatwego dostępu do wszystkich niezbędnych elementów. Warto również zaimplementować systemy kontrolujące spakowane elementy, aby zapobiec pomyłkom w kompletności zawartości kartonów.
Kartoniarka ICMI
Linia do pakowania złożonych mebli
Maszyna firmy SCM do foliowania detali
Możliwe funkcjonalności do wdrożenia:
- System kontroli pakowanych elementów, np. przez skanowanie kodów kreskowych.
- System wizyjny nadzorujący proces pakowania i wykrywający nieścisłości.
- Dodanie kontroli wagi spakowanej by wykrywać braki w paczce.
- Monitorowanie na bieżąco postępu w ilości przygotowanych zamówień.
- Prezentowanie instruktażu dla osoby pakującej w celu poprawnego zabezpieczenia detali.
Korzyści z cyfryzacji:
- Zmniejszenie ilości pomyłek przy pakowaniu.
- Mniej uszkodzeń towaru w transporcie dzięki poprawnemu zabezpieczaniu detali w paczce.
- Skrócenie czasu na skompletowanie zlecenia.
Etap 5: Paletyzacja
Ostatnim etapem procesu produkcji mebli jest ułożenie kartonów na palecie i zafoliowanie całości. Niezależnie od tego, czy towar trafi do magazynu firmy, czy jest realizowany pod konkretne zamówienie, spaletyzowanie jest konieczne, aby ułatwić logistykę i składowanie.
Na rynku dostępnych jest wiele w pełni zautomatyzowanych rozwiązań, które mogą znacząco usprawnić ten etap. Takie systemy wymagają jedynie informacji o wymiarach kartonów, które mają zostać ułożone. Po dostarczeniu tych danych, automatyczne systemy paletyzujące potrafią precyzyjnie układać kartony na palecie i odpowiednio je zabezpieczyć.
Stanowisko paletyzujące z robotem
Paletyzacja paczek z meblami przez robota
Owijarka palet
Możliwe funkcjonalności do wdrożenia:
- Skanowanie kodów kreskowych spakowanych paczek.
- Automatyczne przekazywanie schematów układania paczek przy zmianie zlecenia.
- Monitorowanie ilości spakowanych paczek i palet i przekazywanie informacji do systemu magazynowego.
Korzyści z cyfryzacji:
- Zmniejszenie ilości pomyłek przy pakowaniu.
- Skrócenie czasu przezbrajania systemu.
- Skrócenie czasu na skompletowanie zlecenia.
Najczęściej wdrażana funkcjonalność przez ImpiCode
Monitorowanie produkcji w czasie rzeczywistym
Jednym z kluczowych elementów do wdrożenia w nowoczesnej fabryce meblarskiej jest centralny system monitorowania produkcji. System ten powinien zbierać dane z każdej maszyny produkcyjnej, na każdym etapie produkcji, a najlepiej również posiadać informacje o ilości przygotowanych półproduktów i lokalizacji wszystkich detali w cyklu produkcyjnym.
Podstawową funkcjonalnością jest prezentowanie dziennego planu produkcyjnego oraz wskazywanie nadwyżki/niedoboru względem zaplanowanego wolumenu na daną chwilę. Dostęp do podglądu raportu mogą mieć nie tylko kierownicy i planiści produkcji, ale również wszyscy operatorzy maszyn, np. może być wyświetlany na ekranie tablica andon (ekran) w hali produkcyjnej.
Ponadto mogą być stworzone dedykowane widoki dla operatorów konkretnych maszyn, np. raport z realizacji zlecenia maszyn wiercących, aby w razie potrzeby wesprzeć maszynę pozostającą w tyle. Dla kierowników zmiany proponujemy również raport informujący o zbliżającej się konieczności odebrania/dostarczenia detali pod konkretną maszynę, tak aby nie doszło do zastojów.
Widok w systemie MES z aktualnej produkcji
Podgląd produkcji na piłach
Podgląd systemu składowania - rolek
Dlaczego warto zlecić firmie ImpiCode zbudowanie systemu MES?
- Znajomość branży: Znamy podstawowe etapy produkcji mebli, wiemy z jakimi wyzwaniami mierzą się kierownicy produkcji i rozumiemy używaną terminologię przez Twój zespół. Dzięki temu znacznie łatwiej będzie Ci się z nami dogadać i wdrożyć system intuicyjny dla Twoich pracowników. Posiadamy doświadczenie w automatyce przemysłowej i rozumiemy kluczowe aspekty i wymagania wiążące się z tą branżą.
- Integracja z różnymi maszynami: Programiści w ImpiCode są w stanie połączyć się po dowolnym przemysłowym protokole komunikacyjnym (np. Modbus, Ethernet/IP, Profinet i inne), a także za pomocą integracji przy pomocy plików tekstowych (CSV, XML) czy SQL. Jeśli tylko producent maszyny udostępni nam informacje o sposobie komunikacji, będziemy w stanie podpiąć daną maszynę do systemu.
- Wszechstronność usług: Posiadamy różne zespoły programistyczne specjalizujące się w różnych obszarach IT. Dzięki temu w jednej firmie będziesz mógł zlecić zadania z różnych obszarów, np. stworzenie aplikacji mobilnej, oprogramowania wbudowanego czy zlecenie audytu bezpieczeństwa.
- Niezależność sprzętowa: Budowany przez nas system MES nie jest uzależniony od producenta konkretnych maszyn przemysłowych. Możemy w nim modyfikować dowolną rzecz i dołączać maszyny różnych dostawców, co zapewnia większą elastyczność i przyszłościową skalowalność systemu.
Poznaj firmy, które nam zaufały. Za tą sekcją dalej opisujemy korzyści cyfryzacji.
Nasi klienci
Astor
Adamed
Astorino Kawasaki Robotics
RCC Nova
TU
Bergakademie Freiberg
Eco Light LED
M2M Team
Narodowe Centrum Promieniowania Synchrotronowego SOLARIS
Fundacja AVLab.pl
NowaLed ILL
EMKA Project
IFX Payments
Technische Universität Bergakademie Freiberg to najstarsza akademia górniczo-hutnicza na świecie, założona w 1765 roku. Celem projektu było stworzenie "Mechanicznego Kowala", który będzie obrabiał metal na dostępnych maszynach tak jak aktualni pracownicy.
Stworzyliśmy środowisko programistyczne oparte na RoboDK, w którym programuje się proces wysokopoziomowymi komendami. Oprócz sterowania ramieniem robota musieliśmy także zapewnić synchronizację z maszynami, z którymi robot współpracuje. Projekt został głównie zrealizowany przy użyciu języków programowania Python i C++.
W ramach swojej działalności firma opracowała edukacyjnego robota ASTORINO. Dla którego zbudowaliśmy interpreter języka AS do języka C. Język AS jest używany do programowania robotów Kawasaki.
Jednym z głównych wyzwań technologicznych było stworzenie interpretera, który działa przy minimalnym zużyciu pamięci RAM i jest uruchamiany na mikrokontrolerze robota.
Śpij spokojnie dzięki systemom predykcji od ImpiCode
Prognoza i zapobieganie możliwym awariom
Dzięki nowoczesnym systemom monitorowania z funkcją predykcji awarii, można skutecznie przewidywać awarie maszyn na podstawie zgromadzonych danych. Takie systemy dają możliwość wcześniejszego zamówienia niezbędnych części i zaplanowania serwisu maszyny jeszcze przed wystąpieniem problemu, co minimalizuje ryzyko przestojów produkcyjnych i zwiększa efektywność operacyjną.
Podstawą efektywnej predykcji awarii jest ciągłe monitorowanie parametrów pracy maszyn, takich jak wibracje, temperatura czy prędkość obrotowa. Dane te, zbierane w czasie rzeczywistym, pozwalają na identyfikację trendów i wykrycie anomalii, które mogą wskazywać na zbliżającą się awarię. Na przykład wzrost wibracji może sugerować problemy z łożyskami lub niewłaściwe wyosiowanie, natomiast wzrost temperatury może wskazywać na zwiększone tarcie i drobne uszkodzenia mechaniczne.
Często do zebrania niezbędnych danych konieczne jest dokupienie i zamontowanie dodatkowych czujników w maszynach. Czujniki takie potrafią generować znaczące ilości danych (np. wykres przebiegu drgań), co wymaga systemu o dużej przepustowości. Dlatego warto jest wybrać firmę programistyczną ImpiCode, która ma doświadczenie w obróbce dużych strumieni danych.
Oprócz systemu predykcji awarii, możliwe jest wdrożenie inteligentnego harmonogramu serwisowego. System taki prowadzi spis wszystkich czynności serwisowych (od serwisu maszyny po wymianę osprzętu) wraz z liczbą przepracowanych godzin. Można również monitorować inne metryki, takie jak ilość wyciętych otworów, dokładny czas pracy osprzętu, czy łączną długość przeciętych materiałów. Dzięki tym metrykom, harmonogram prac serwisowych może być bardziej szczegółowy i precyzyjny, co pozwala na lepsze planowanie i unikanie niespodziewanych awarii.
Porozmawiaj z nami o swojej fabryce
Jeśli rozważasz wdrożenie systemów informatycznych w swojej fabryce, lub jeśli obecnie wdrożony system nie został w pełni zintegrowany (np. nie wszystkie maszyny zostały podłączone), skontaktuj się z nami. Jako Twój partner technologiczny, wspomożemy Cię w rozbudowie i automatyzacji Twojej fabryki.
Nawet jeśli planujesz wdrożyć system innej firmy, ale wiesz, że będziesz potrzebował dodatkowych integracji, zgłoś się do nas. Będziemy Ci towarzyszyć w tym procesie. Już na etapie wdrażania systemu przez inną firmę nawiążemy z nimi współpracę, aby dalsza integracja, którą nam powierzysz, przebiegła sprawnie i efektywnie.
Skontaktuj się z nami, aby dowiedzieć się więcej o tym, jak możemy wesprzeć rozwój Twojej fabryki.
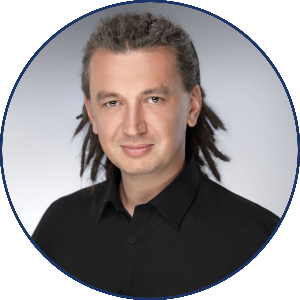
Jako współzałożyciel ImpiCode, posiadam wieloletnie doświadczenie w tworzeniu dedykowanych systemów, zarówno na poziomie biznesowym, jak i technologicznym.
Z przyjemnością podzielę się moją wiedzą technologiczną z Tobą, by usprawnić produkcje w Twojej fabryce.
Jako współzałożyciel ImpiCode, posiadam wieloletnie doświadczenie w tworzeniu dedykowanych systemów, zarówno na poziomie biznesowym, jak i technologicznym.
Z przyjemnością podzielę się moją wiedzą technologiczną z Tobą, by usprawnić produkcje w Twojej fabryce.